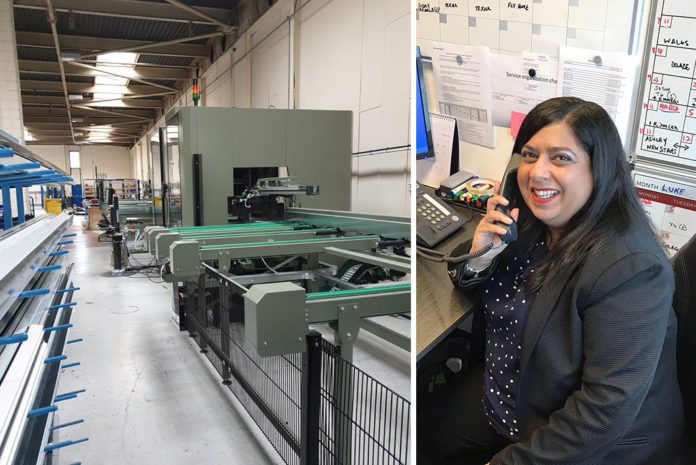
Emmegi (UK) says it has made significant investments in its service team over the past year, appointing Kully and Wayne Hunter to manage service and operations, and increasing the size of its onsite engineering team to seven.
According to Emmegi (UK), the response from customers would suggest that this is paying dividends, with ‘lots of positive feedback’ on how quickly service issues are now being resolved and how effectively Emmegi is now training customers to get more from their machines, whilst also trying to eliminate avoidable breakdowns.
Alongside its own onsite team, Emmegi (UK) adds that it has contracted a team of engineers from its Italian HQ to work in the UK for the next year, and is extending its use of remote servicing on software in particular so that specialists based in Italy can dial into a customer’s machine set up and ‘very quickly’ resolve any issues.
Wayne Hunter explained: “Just by working a little bit smarter, we are now resolving issues for more customers, more quickly. Our processes are more efficient, but we are also taking a more proactive rather than reactive approach, which is already delivering better value for customers.”
A typical recent example is at TWR Group in County Durham where Emmegi installed a new Quadra L1 machining centre in July 2019. When TWR contacted Emmegi (UK) with a series of queries on the machine, Emmegi despatched two of its engineers to review how it was being operated and to provide training and advice.
The company says that it advised the team at TWR on positioning of the gripper height and clamp setting adjustment to avoid lengths from being cut incorrectly and discussed how to maximise the infeed magazine capacity so that batching and sub batching of jobs is more efficient.
TWR is reported to have made their principle machine operators available for a dedicated training session with Emmegi’s senior engineer, Garry Barehead and, as a result, TWR is said to be happy that its Quadra is now running ‘faster and better’ and delivering an improved return on investment.
The same smart working approach reportedly helped another customer recently when they had a problem with their Satellite XT. Kully ensured that Emmegi solved the problem within 90 minutes of it being reported by utilising an engineer who was able to dial in and diagnose almost immediately that the MG pilot was simply disconnected.
Similarly, PSP Aluminium were reported to be ‘back up and running’ within 75 minutes of reporting an error message on their X6 CNC machine when Kully asked Emmegi in Italy to dial in and remotely recover a file folder which had gone down.
Wayne added: “We are encouraging customers to send us videos of faults so that we can diagnose and respond more effectively. Sometimes, of course, we are finding that there isn’t even really a fault – it is simply that the machine hasn’t been set up correctly or the operator hasn’t been adequately trained. In these cases, we can provide instructions direct from the service centre in Coventry to save time and get customers up and running really quickly, or send out engineers to give more detailed advice and training, with the overall aim of helping customers to achieve a more reliable and efficient operation.”