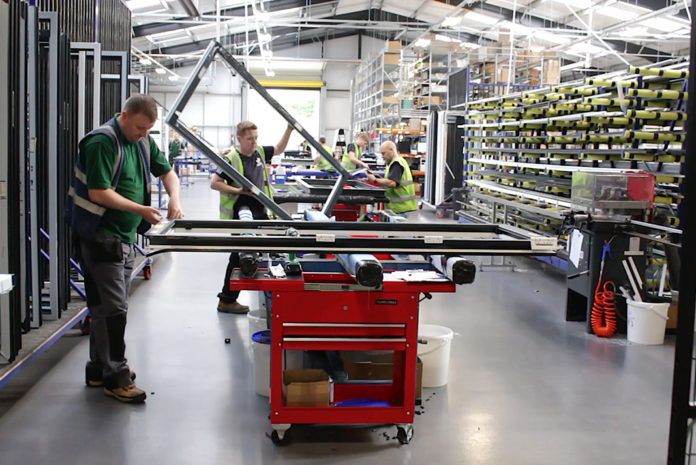
Sternfenster has appointed 30 new members to its manufacturing team in less than three months as part of a strategy to rapidly build capacity in response to the exponential growth in demand seen for windows and doors this summer.
Accompanied by continuing investment in plant and machinery, the trade specialist says the new posts give ‘immediate new flexibility’ within its operation, plus support its strategy for long term growth.
Mike Parczuk, managing director, Sternfenster: “Our focus has been to invest and bring a high degree of automation to our manufacturing capability. This gives us the flexibility to switch-on increased capacity as we need it.
“The limiting factor on that capacity is people. There are jobs that can’t be done without them – however, advanced your operation is.
“With our team fully back from furlough in June, it became clear that we were going to need to recruit to meet demand, which we’ve been able to do successfully and importantly, inline with our plans for longer term growth.”
This and its partnership with Deceuninck, Mike said, had meant that Sternfenster had in large, been able to maintain lead times on foiled products.
Manufacturing Deceuninck’s 2500 Heritage chamfered and 2800 sculptured systems, plus it’s Heritage flush casement, these are available in 30 colour options, plus from Sternfenster, in a StyleLine Graf seamless-welded finish.
“I’m not going to tell you that we came through completely unscathed, because we were,” Mike continued, “but our profile supply chain for the most part held up and with the capacity gains that our recruitment strategy has given us, we were able to maintain supply on foils within what I believe were pretty reasonable time frames.”
While building its headcount, Sternfenster has also continued to invest in machinery. This includes a six-figure investment in a new Schirmer ALU BAZ Composite Orbit-C machining and cutting centre and a FOM Ever Theta crimping machine.
“We’re investing in people but also machinery,” Mike explained. “We don’t want to use them for cutting, prepping and crimping because people – because they are people, and not machines – don’t give you the consistent product quality that we’re looking for.
“The Schirmer brings exceptional quality right to the start of our aluminium manufacturing process. The Ever Theta Crimper, which will come in later this autumn, gives us the same consistent quality, while further expanding our aluminium capacity.”
Sternfenster committed to a £3.6m investment in a dedicated aluminium manufacturing facility in 2017. With a 30,000ft2 shop-floor footprint, plus 10,000ft2 of office space, this includes its own powder coating line.
This and its recruitment strategy, meant that it was also able to maintain lead times on its Smarts bi-fold and inline sliding door offers.
“We don’t expect demand to stay where it is – but we do expect growth overall, to continue into next year, and we have a strategy in place for that, which includes investment in machinery but also people.
“We remain a family owned and run business, and the people who work here define who we are. You can have the best machinery or products in the world but if you don’t underpin that with the right service, you aren’t going to get very far.”